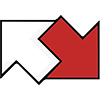
Blastroom TruGlide Abrasive Recovery Floor
Engineered and built to increase your production output whilst minimising running cost.
KIS Inspired Recovery Floor
After buying several abrasive recovery floor systems, and on selling them to our customers, we ended up in a heap of trouble. The floors were complicated and unreliable. Forever breaking down and causing blasting production slow downs. So we went back to the drawing board to develop our own abrasive recovery floor.
The nature of abrasive blasting is aggressive and hard wearing. So our design philosophy is always to KIS (Keep It Simple). Priority for the floor was it must be a simple operation and with minimal moving parts. From bitter experience we had learned moving parts such as bearings and air cylinders, inside the blastroom, do not mix well with abrasives. Secondly the floor has to be modular so it is quick and easy to install, and without extensive deep foundations.
A blastroom is a long term investment and will be used for many years. Therefore the abrasive recovery floor should also be cheap to operate and easy to maintain.With the above parameters as our guide we developed the TruGlide Abrasive Recovery Floor.
Modular Bolt Together Floor
The recovery floor is manufactured from a series of modular floor channels that sit into a 380mm deep foundation. For quick and easy installation on site, the floor channels are modular and simply bolt together. The whole floor can easily be assembled in one day.
During blasting a 10mm thick protective layer of abrasive forms in the bottom of the floor channels. This layer of abrasive creates a wear resistant barrier, to protect the recovery floor channels from wear.
Hardened Steel Blades Recover Grit
Each floor channel is fitted with a lightweight rack assembly containing a hardened steel blade. The rack assembly repeatedly travels up and down the entire length blastroom. The racks are driven by a single digit kw motor. On its' forward stroke the hardened steel blade is lowered into to position to skim off a thin layer of abrasive settled in the floor channel. On its' reverse stroke the hardened steel blade is raised and positioned above the layer of abrasive, as the blade reverses to the far end of the blastroom.
This forward and reverse cycle operates automatically and continuously to recover the recently blasted abrasive. At the end of the forward stroke is a cross screw or belt conveyor. Once deposited into this, the abrasive is recovered and cleaned of dust and debris. The cleaned abrasive is then stored above the blast pots ready for reuse.
Less Wear and Tear Increases Reliability
The rack and blade assemblies ride on delrin blocks. As they are constantly traveling the racks are only exposed to flying abrasive for a brief few seconds on every stroke, as they pass below the blaster. This, combined with the protective layer of abrasive in the floor channel, virtually eliminates wear and tear. Less wear and tear equates to more reliability. More reliability enables the floor to operate continuously day after day, week after week. A few simple checks and adjustments, once monthly, are all that is required to keep the floor operating.
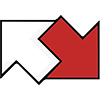
How It Works
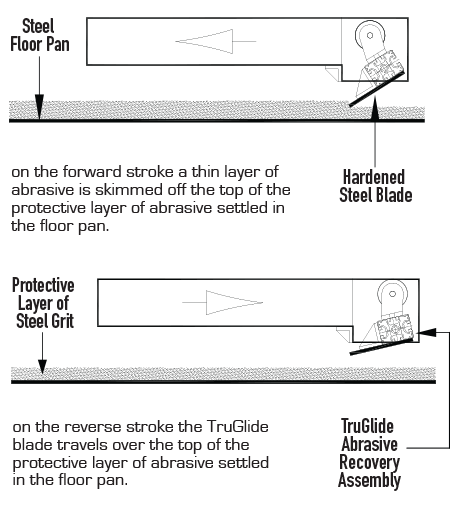
No Moving Parts Reduces Wear
Moving parts and hard abrasive do not mix well in a blastroom. The TruGlide Abrasive Recovery Floor virtually eliminates all moving parts from inside the blastroom.
Below the blastroom perforated floor grid are a series of recovery channels into which blasted abrasive and waste fall. A layer of abrasive 10mm thick lines the bottom of each channel. This abrasive forms a wear resistant layer to protect the floor from wear. Each channel is fitted with a tough powder coated rack assembly containing a hardened steel blade that travels up and down the length of the blastroom to recover the abrasive and removed contaminants.
Continuous Running for High Production As the TruGlide recovery blades are constantly moving they are only exposed to flying abrasive for a brief few seconds on each stroke. This feature, along with the protective layer of abrasive in each channel, virtually eliminates wear and tear. This allows the recovery floor to run continuously day in and day out to keep up with the most demanding production schedules. More production equates to more revenue.
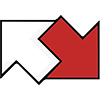
TruGlide Abrasive Recovery Floor Configuration
TruGlide Abrasive Recovery Floors are built in various configurations to suit your operating and production requirements. Illustrated here are some typical installation options. Floors are tailor made to perfectly match your requirements.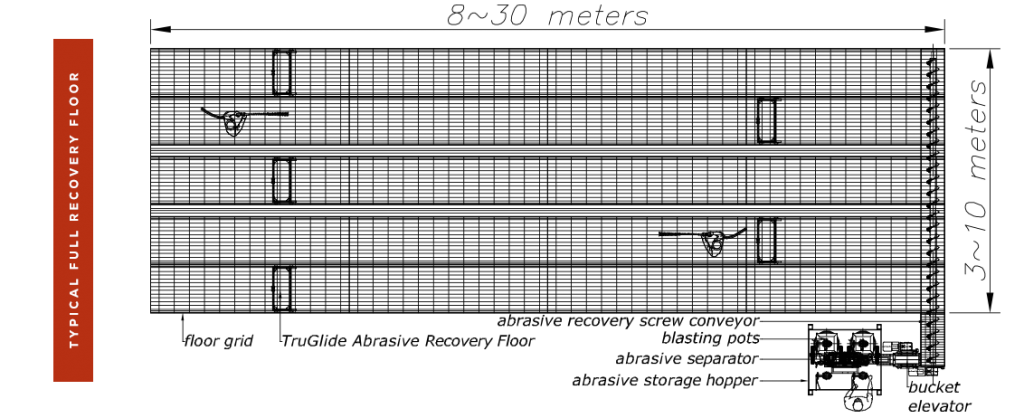
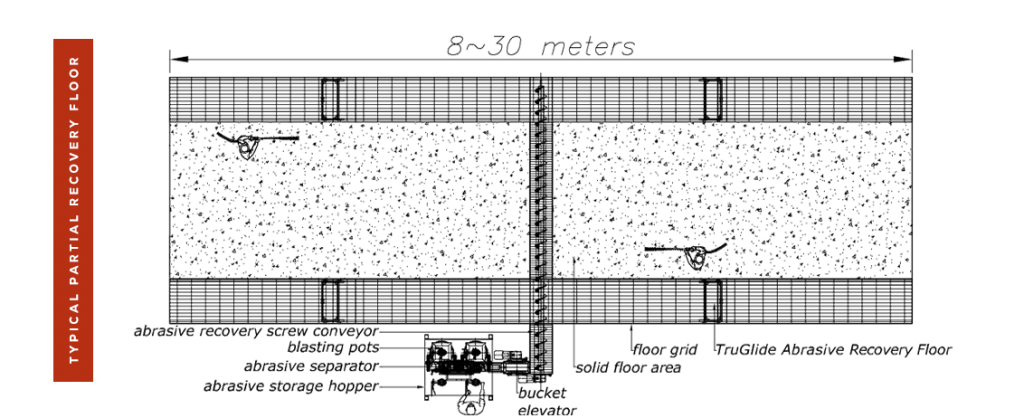
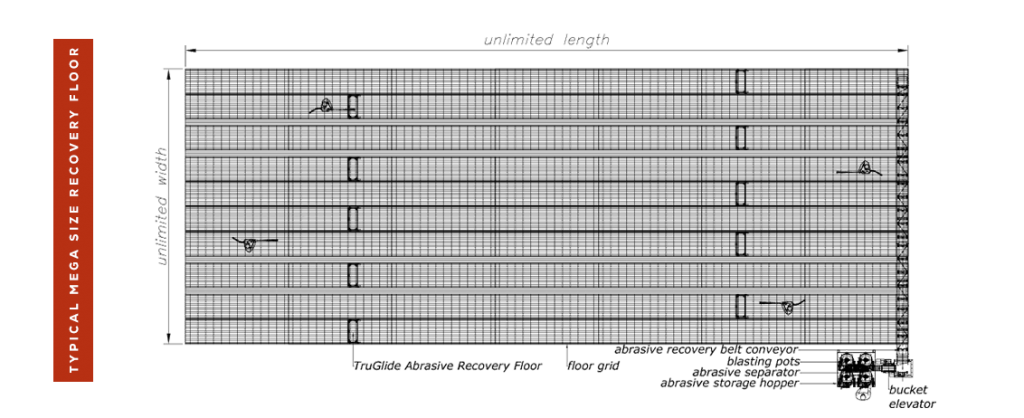
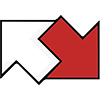
TruGlide Abrasive Recovery Floor KIS
The TruGlide Abrasive Recovery Floor does not require a lot of materials to make, therefore we can keep the costs down and sell to you cheaper. Our scope of supply also includes steel floor pans and grating so you won't have any unpleasant hidden cost surprises having to supply these items yourself.
The TruGlide Abrasive Recovery Floor is a modular bolt together design. You supply a simple concrete foundation, to our design, and we will drop in the floor and bolt it together. The recovery floor is quick and easy to install. Within a very short period you will be up and running and blasting in production.
The simple concept of minimal moving parts inside the blastroom ensures the TruGlide Abrasive Recovery Floor keeps on running. Press the start button and start blasting and the recovery floor will take care of returning and cleaning the abrasive ready for reuse. The floor design ensures minimal maintenance is required. Occasional maintenance and adjustment with basic hand tools is all that is required.
The TruGlide Abrasive Recover Floor is extremely energy efficient. Full floor abrasive recovery can be achieved in small blastrooms for <10kw. Even very large blastrooms require only <15kw for full floor recovery. This minimal power requirement can provide abrasive recovery for multiple blasters and is a fraction of the power required for pneumatic and vacuum recovery systems. The TruGlide Abrasive Recover Floor will provide you with substantial yearly power bill savings.
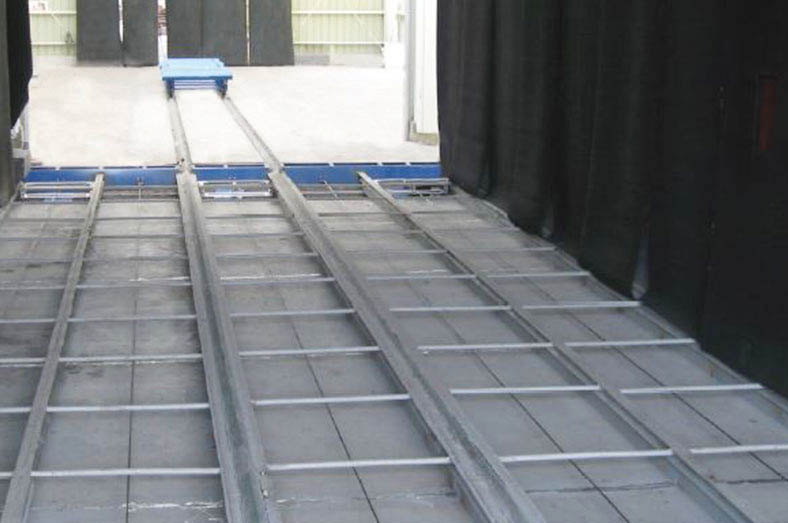
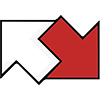
Previous Projects
TruGlide Floor Project by Blastechnik