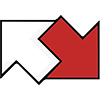
Blastroom Abrasive Recycling
Critical to quality surface finishing, and high production blasting, is keeping the abrasive clean. After every cycle the abrasive must be recycled and any dust and oversize waste removed from it, ensuring the abrasive that exits the nozzle is as good as new.
The TruGrit Blastroom is fitted with a multi stage separator to achieve this. Recovered abrasive, dust and debris is fed into the separator from the bucket elevator.
The first stage of separation is the rotary scalping drum to separate rust flakes, paint flakes, trash and other oversize contaminants from the abrasive. This is separated and deposited into a waste bin via waste chute.
The second stage of separation is to remove fines and dust from the good abrasive. A gravity fed air-wash cascades the abrasive and dust through a ventilation air stream. Dust and fines are drawn out to the dust collector, by the powerful air stream, whilst good reusable abrasive falls into an abrasive storage hopper ready for reuse.
This separator ensures only correctly sized good reusable steel grit is returned to the blast pots, which results in higher production rates, lower operating costs and highest quality work piece finishing.
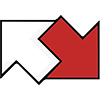
Previous Projects
Abrasive Recycling Project by Blastechnik